Actemium’s control system expertise at the service of sustainable innovations
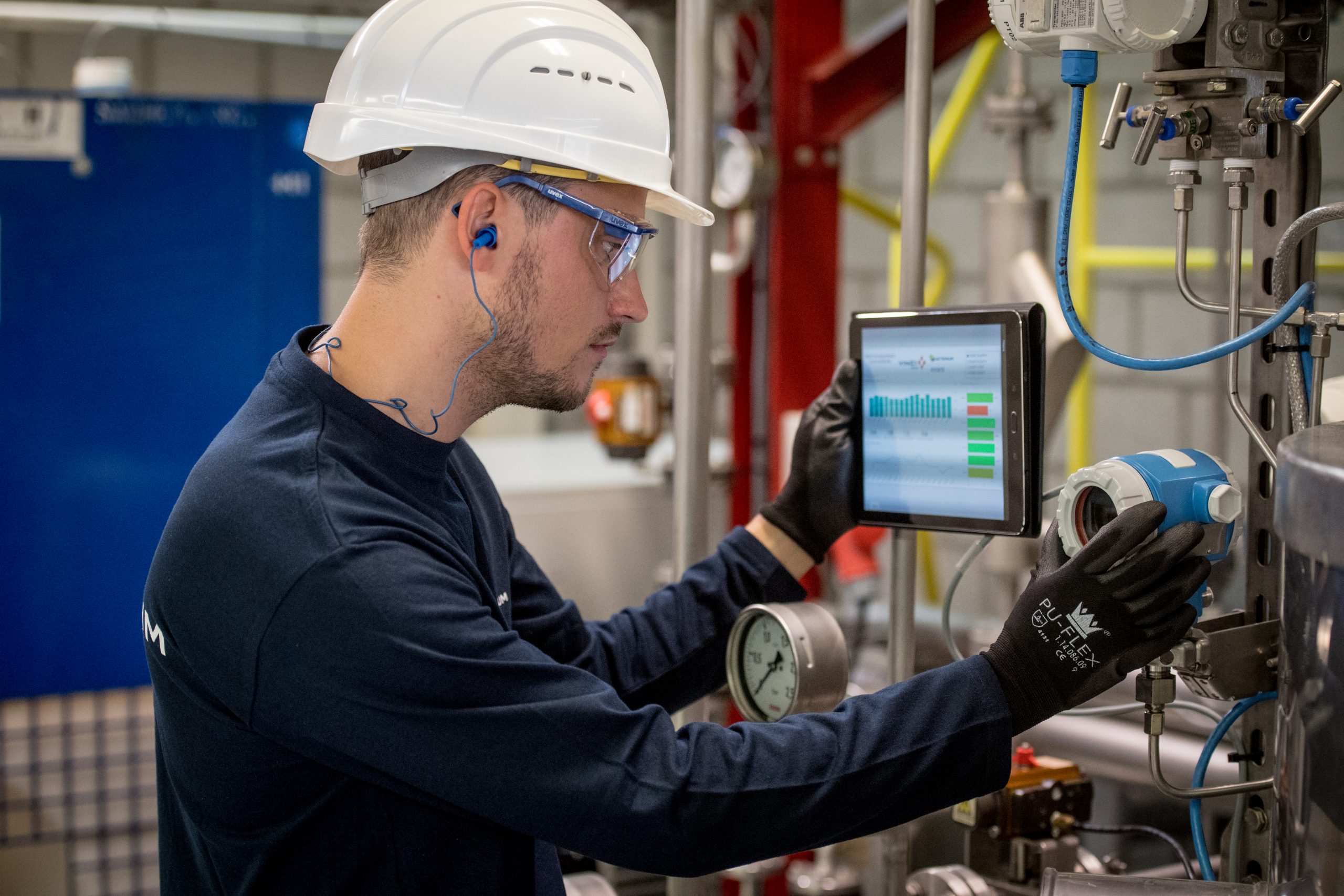
The energy sector faces significant environmental challenges in electricity production, driving power-generating facilities to seek sustainable solutions. In this context, Actemium recently contributed to a project dedicated to biomass fuel production allowing electricity generation in the United Kingdom.
Biomass, a promising renewable energy source
Biomass is a renewable organic material derived from plants or animals waste that can be converted into biofuel through various processes and is increasingly being used as an energy source.
In North East England, a power-generating facility implemented a Biomass Fuel Handling System (BFHS) constructed at a port site, following a simple process: the fuel is first unloaded from ships onto conveyors and then deposited into one of three storage silos. After storage, the fuel is decanted and transported via conveyor to a rail-loading silo for eventual shipment by train to the power station.
The client needed to automate this process’ control system, and entrusted Actemium Automation Yorkshire to do so. The control system had to meet several requirements: ensuring target load figures, assisting operators, and monitoring key parameters such as moisture content, material weight, CO2 levels, temperature and others.
Real-time control system to ensure safety and efficiency
To meet these expectations, the Actemium team developed, tested, and commissioned a PLC-based site-wide control system to command, monitor, and record the movement of biomass pallets from the quayside to storage silos and the rail-loading facility. The process used a Rockwell ControlLogix Safety platform with a SCADA control system, operated from a dedicated room at the port where the power plant is located. This system requires minimal manual intervention, prioritising automation and ensuring efficiency.
Innovative solutions and sharp results
Actemium’s expertise and dedication resulted in an automated system that monitors plant’s operations allowing personnel to track the transportation and storage of biomass in real-time and achieve a maximum flowrate of 850 tonnes/hour.
This automation was a crucial step for our client, enabling them to transport fuel safely and efficiently while ensuring the reliability of power generation. This project highlights Actemium’s ability to overcome complex challenges and deliver sustainable solutions in the energy sector.