Enhancing Production & Safety: Retrofit Success at Advanced Medical Solutions
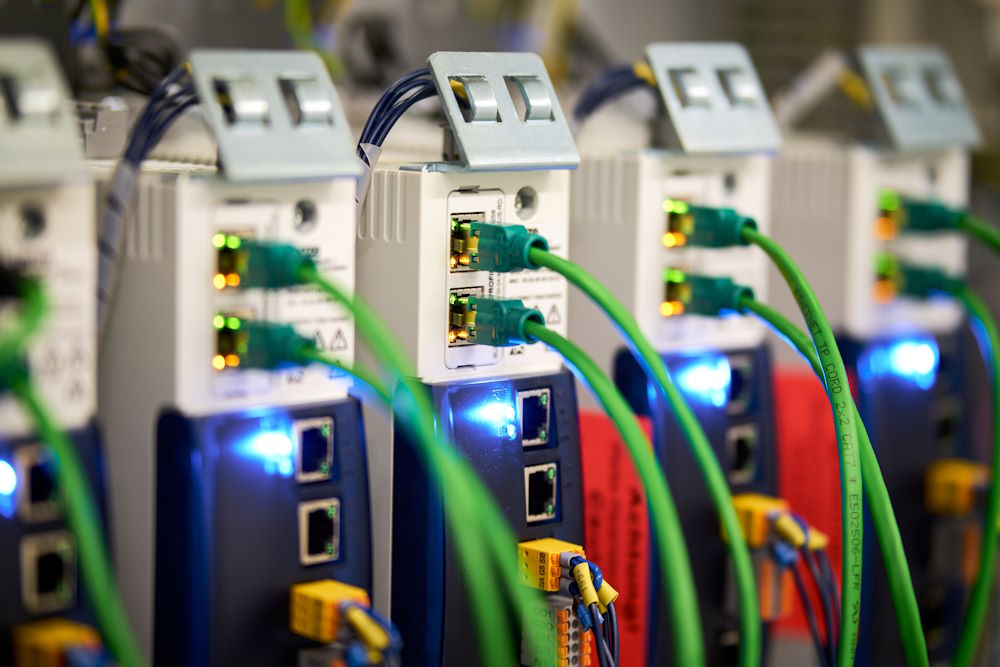
Advanced Medical Solutions BV in Etten-Leur is part of a British developer and manufacturer of advanced wound care products. Two critical production processes at this company are the production and cutting of high-quality polyurethane foam (PU). In order to continue to guarantee delivery reliability in the future, the entrusted Actemium to perform a retrofit of one of the production line.
Risk Assessment and Optimised Production Control
At Advanced Medical Solutions, long rolls of high-quality polyurethane foam are produced, which are then sawn into thicknesses of 1.5 to 10 millimeters and then cut into the desired width. The result is the basis for extremely absorbent wound care products for professional healthcare.
Actemium first carried out an extensive risk inventory and machinery evaluation, then started making all production processes future-proof in phases, based on a priority list.
The risk assessment identified, among other things, the need to optimise the servo and frequency controllers of the foam line to ensure long-term reliability and future readiness.
The foam line is the most business-critical part of our production, which is why we focused on optimising the control of this part with Actemium
says Site Operations Manager Frank Maas.
Expanded Long-Term Partnership
Actemium Netherlands has been Advanced Medical Solutions BV’s service provider for various technical installations for many years. This long-term partnership allowed Actemium teams to gather precious knowledge and experience with the company’s industrial automation and electronic controls.
As part of the functional inventory, we added the optimisation of the ‘as-built’ drawing package to their project scope. As a Maintenance Engineer, it is pleasant to work with an expert and experienced partner like Actemium.
says Bas van Loon.
Major Breakthroughs From Retrofit
Retrofit offered major benefits and the most significant ones being safety for all employees, delivery reliability for customers and a step towards sustainability in the overall production process.
We learned a lot from Actemium’s test setup, which prevented unnecessary downtime during the conversion. Actemium has been an exceptionally knowledgeable and experienced partner in all phases of our project and has dealt with our production planning with great flexibility.
concludes Maas.