Reconditioning graphite exchangers: Actemium’s unique expertise
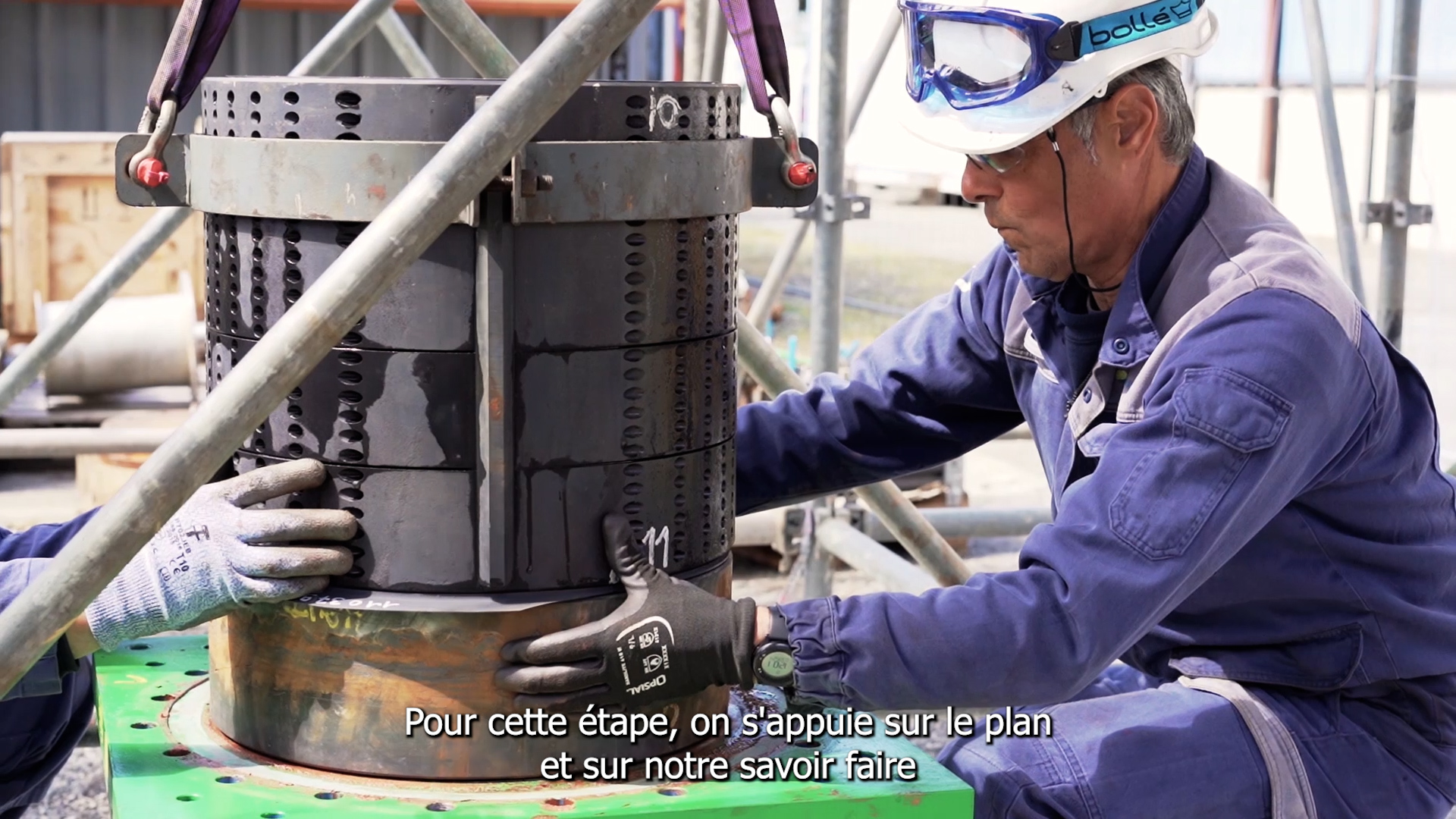
Graphite exchangers are sensitive pieces of equipment used in a variety of manufacturing processes. Actemium Adour Mécanique, based in southern France, maintains these important machines for a variety of customers in the chemical and pharmaceutical industries. Graphite is an amazing material, heat conductive and highly resistant to chemical corrosion. But the graphite in these exchangers, like the “lead” in your pencils, is brittle and fragile.
Often handled by the manufacturers, reconditioning graphite exchangers requires highly specialized know-how that Actemium Adour’s teams have acquired over the twenty years since one of the major manufacturers first came to them for support.
Safety and coordination at every stage
Reconditioning requires special equipment including lifting collars, cranes, torque tightening equipment, and, of course, industrial steam generators for testing.
First the team studies the specific characteristics of the exchanger they are going to recondition. Then they plan the operating procedure. Getting a tower in place for maintenance and extracting the core are high-risk operations that require close coordination among the technicians.
Careful orchestration of the technicians and tools is key, and safety comes first at every stage.
The expert technicians examine each graphite block and every used part before replacing or repairing them. Each block goes through visual inspection and pressure testing. Then the blocks are restacked and the fluid circuit is reinstalled.
Finally, everything is fitted and torque tightened according to the manufacturer’s specifications. Steam injection heating and final tests validate the reconditioning.
Flexible working procedures
The crew at Actemium Adour services a large variety of exchangers, both cylindric and cubic, either at their facility or the customer’s site, depending on the type of exchanger.
Actemium Adour Mécanique has developed and maintained this highly specific know-how over two decades, and a new employee will spend as many as five years learning the procedures before they can take charge of this maintenance protocol.