Vencosteel’s Digital Transformation: A Case Study in Manufacturing Excellence
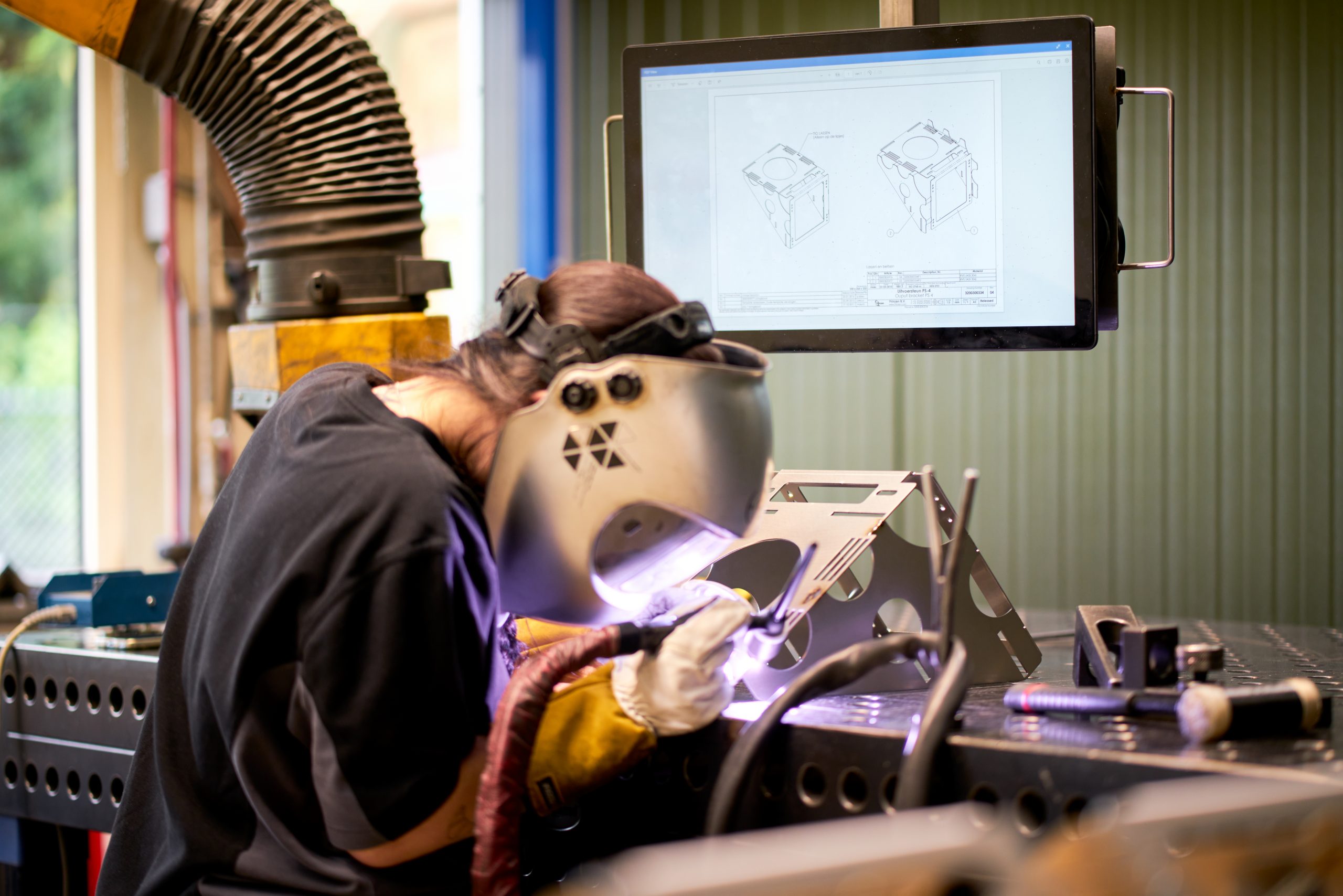
Vencosteel, part of the Vencomatic Group, produces metal components for chicken coop equipment in Eersel, Netherdlands,. Using a laser or punching machine, products are cut from large metal sheets and then processed further. To precisely locate the products, operators needed enormous paper flows, involving a lot of searching and actions.
The company wanted to switch to paperless working, gain more insight into machine performance and improve the material flow on the shop floor. To do so, Vencosteel approached Actemium in 2020 to think about the implementation of an MES (Manufacturing Execution System).
Many systems to connect
The assignement was challenging. Making multiple systems communicate with each other required close cooperation between different parties, including Vencomatic Group, Vencosteel and suppliers of software and machines. Actemium created machine interfaces for all of Vencosteel’s press brakes, laser, punching and other machines and enabled communication between the MES and SAP as an ERP system.
Efficency gained and time saved
Orders from SAP, information from the machines,3D and 2D CAM program Cadman-B and nesting software WiCAM are coming together in the MES. As a result, the work preparation is fully digitalized and 100,000 to 150,000 order prints are eliminated annually. A significant saving in paper! Actemium trained the team leaders at Vencosteel, who in turn taught the operators how to work with the new system.
Their work has become clearer. They know immediately where the products they have to process are. They can also view 3D drawings of the products they have to make in the MES.
details Nick Verstegen, lead engineer at Actemium
The MES does the planning in all the separate departments based on all the different parameters: diameter, material type, urgency, tongue-groove combination or combination of edge tools. Furthermore, the operator has access to all the necessary information from his workplace and that information can easily be expanded.
World of difference
The number of production orders at Vencosteel has increased from 25,000 in to 34,000 in four years. Thanks to the digitalisation process, the company can process this volume with the same number of work planners.
We have significantly improved the efficiency of our processes and shortened the lead times in work preparation and production. This has increased our delivery reliability: we can serve customers better. We have also noticed that there are far fewer pallets on our production floor. A world of difference.
says Bart Coppens, manager Vencosteel at Vencomatic Group.
For Actemium, this was the first sheet metal project in paperless working. Vencosteel has now demonstrated the system to other companies that are active in the same sector.